Wybór sprzętu zapewniającego najwyższą jakość i produktywność podczas spawania to nie tylko źródło prądu czy uchwyt spawalniczy – ważną rolę odgrywają również materiały eksploatacyjne. W szczególności wskazówki kontaktowe mogą znacząco wpłynąć na efektywność procesu i naliczanie przestojów w celu usunięcia problemów. Wybór właściwej końcówki prądowej do danego zadania może również mieć wpływ na rentowność operacji spawania.
Końcówki prądowe odpowiadają za przenoszenie prądu spawania na drut podczas jego przejścia w celu wytworzenia łuku. Optymalnie drut powinien przechodzić z minimalnym oporem, zachowując jednocześnie kontakt elektryczny.
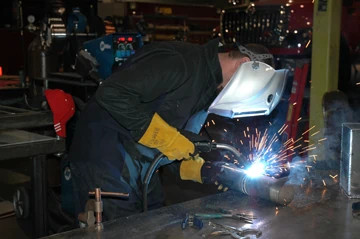
Końcówki kontaktowe mogą znacząco wpłynąć na efektywność procesu spawania i wydłużanie czasu przestojów w celu usunięcia problemów, a także mogą mieć wpływ na rentowność operacji spawania.
Z tego powodu zawsze ważny jest wybór końcówki prądowej wysokiej jakości. Chociaż produkty te mogą kosztować nieco więcej niż produkty gorszej jakości, istnieje długoterminowa wartość zanegowania tej ceny zakupu z góry.
Co więcej, końcówki kontaktowe wyższej jakości są zazwyczaj obrabiane maszynowo z węższymi tolerancjami mechanicznymi, tworząc lepsze połączenie termiczne i elektryczne. Mogą również mieć gładszy otwór środkowy, co skutkuje mniejszym tarciem podczas przechodzenia drutu. Oznacza to spójne podawanie drutu przy mniejszym oporze, co eliminuje potencjalne problemy z jakością.
Końcówki prądowe wyższej jakości mogą również pomóc zminimalizować przepalanie (tworzenie się spoiny wewnątrz końcówki prądowej) i zapobiegać powstawaniu błędnego łuku spowodowanego nierównomierną przewodnością elektryczną. Zwykle wytrzymują też dłużej.
Wybór odpowiedniego materiału i rozmiaru otworu
Końcówki prądowe stosowane w półautomatycznym spawaniu MIG są zazwyczaj wykonane z miedzi. Materiał ten zapewnia dobrą przewodność cieplną i elektryczną, umożliwiając równomierne przekazywanie prądu do drutu, a jednocześnie jest wystarczająco trwały, aby wytrzymać ciepło wytwarzane podczas procesu spawania. Do spawania zrobotyzowanego niektóre firmy decydują się na stosowanie bardziej wytrzymałych końcówek prądowych z chromu i cyrkonu, ponieważ są one twardsze niż miedziane i lepiej wytrzymują dłuższy czas zaświecenia łuku w zastosowaniach zautomatyzowanych.
W większości przypadków najlepsze rezultaty daje użycie końcówki prądowej dopasowanej do rozmiaru drutu. Jednakże, gdy drut jest podawany z bębna (np. drut o wadze 500 funtów i więcej) i/lub gdy używany jest drut lity, zbyt mała końcówka prądowa może poprawić wydajność spawania. Ponieważ drut z bębna jest zwykle mniej odlewany, przechodzi przez końcówkę stykową z mniejszym kontaktem lub bez niego — mniejszy otwór wywiera większy nacisk na drut, tworząc większą przewodność elektryczną. Jednakże zbyt mały rozmiar końcówki prądowej może zwiększyć tarcie, co może skutkować nieprawidłowym podawaniem drutu i potencjalnym spalaniem.
I odwrotnie, użycie zbyt dużej końcówki może zmniejszyć przepływ prądu i zwiększyć temperaturę końcówki, co może również prowadzić do spalenia drutu. W razie wątpliwości dotyczących wyboru końcówki prądowej o odpowiednim rozmiarze należy skonsultować się z zaufanym producentem materiałów eksploatacyjnych lub dystrybutorem materiałów spawalniczych.
Najlepszą praktyką jest zawsze sprawdzanie połączenia pomiędzy końcówką kontaktową a dyfuzorem gazu, aby mieć pewność, że jest pewne. W związku z tym bezpieczne połączenie zmniejsza opór elektryczny, który może prowadzić do przegrzania.
Zrozumienie zagłębienia końcówki prądowej
Wgłębienie końcówki prądowej odnosi się do położenia końcówki prądowej w dyszy i jest ważnym czynnikiem wpływającym na jakość spoiny, produktywność i koszty operacji spawania. W szczególności prawidłowe wgłębienie końcówki stykowej może zmniejszyć ryzyko nadmiernych rozprysków, porowatości i przepalenia lub wypaczenia cieńszych materiałów. Może również pomóc zminimalizować ciepło promieniowania, które mogłoby spowodować przedwczesną awarię końcówki prądowej.
Wgłębienie końcówki stykowej bezpośrednio wpływa na wysunięcie drutu, zwane także przedłużeniem elektrody. Im większe wgłębienie, tym dłuższy odstęp i wyższe napięcie. W rezultacie sprawia to, że łuk jest nieco mniej stabilny. Z tego powodu najlepszy występ drutu jest zazwyczaj najkrótszy dopuszczalny w danym zastosowaniu; zapewnia bardziej stabilny łuk i lepszą penetrację niskiego napięcia. Typowe położenia końcówki stykowej to wgłębienie 1/4 cala, wgłębienie 1/8 cala, płaskie i przedłużenie 1/8 cala. Aby zapoznać się z zalecanymi zastosowaniami każdego z nich, patrz Rysunek 1.
Wgłębienie/przedłużenie | Natężenie w amperach | Wystający drut | Proces | Notatki |
1/4 cala Wgłębienie | > 200 | 1/2 – 3/4 cala. | Spray, impuls wysokoprądowy | Drut z rdzeniem metalowym, transfer natryskowy, gaz mieszany bogaty w argon |
1/8 cala Wgłębienie | > 200 | 1/2 – 3/4 cala. | Spray, impuls wysokoprądowy | Drut z rdzeniem metalowym, transfer natryskowy, gaz mieszany bogaty w argon |
Spłukać | < 200 | 1/4 – 1/2 cala. | Impuls krótkoprądowy, niskoprądowy | Niskie stężenie argonu lub 100% CO2 |
1/8 cala Rozszerzenie | < 200 | 1/4 cala | Impuls krótkoprądowy, niskoprądowy | Trudno dostępne złącza |
Wydłużenie żywotności końcówki prądowej
Awaria końcówki prądowej może wynikać z wielu czynników, w tym przepaleń, zużycia mechanicznego i elektrycznego, złej techniki spawania przez operatora (np. zmian w kącie uchwytu i odległości końcówki stykowej od roboczej [CTWD]) oraz ciepła odbitego od materiał bazowy, który jest powszechny w przypadku trudno dostępnych połączeń spawanych lub obszarów o ograniczonej przestrzeni.
Jakość użytego drutu może również wpływać na żywotność końcówki prądowej. Drut złej jakości często ma niepożądany odlew lub spiralę, co może powodować nieregularne podawanie. Może to uniemożliwić prawidłowe połączenie drutu i końcówki stykowej przez otwór, co w konsekwencji skutkuje niską przewodnością i wysoką rezystancją elektryczną. Problemy te mogą prowadzić do przedwczesnej awarii końcówki prądowej z powodu przegrzania, a także złej jakości łuku. Aby przedłużyć żywotność końcówki prądowej, należy rozważyć następujące kwestie:
• Aby zapewnić płynne podawanie drutu, należy używać odpowiednich rolek napędowych.
• Zwiększ prędkość podawania drutu i wydłuż CTWD, aby zminimalizować przepalanie.
• Wybierz końcówki kontaktowe o gładkiej powierzchni, aby zapobiec zaczepianiu drutu.
• Przytnij prowadnicę uchwytu MIG do odpowiedniej długości, aby drut przechodził prawidłowo.
• Jeśli to możliwe, niższe temperatury robocze, aby zmniejszyć zużycie elektryczne.
• Jeśli to możliwe, używaj krótszych kabli zasilających, aby uzyskać płynniejsze podawanie drutu. Jeśli potrzebne są dłuższe kable zasilające, staraj się zminimalizować liczbę pętli, aby zapobiec załamaniom.
W niektórych przypadkach może być pożądana zamiana uchwytu MIG na chłodzony wodą, aby zapewnić dłuższą trwałość materiałów eksploatacyjnych, w tym końcówki prądowej.
Firmy powinny również rozważyć śledzenie zużycia końcówek kontaktowych, odnotowywanie nadmiernej wymiany i odpowiednie postępowanie zgodnie z niektórymi sugerowanymi środkami ostrożności. Rozwiązanie problemu tego przestoju wcześniej niż później może znacznie pomóc firmom w zmniejszeniu niepotrzebnych kosztów związanych z zapasami, przy jednoczesnej poprawie jakości i produktywności.
Czas publikacji: 04 stycznia 2023 r