Porowatość, czyli nieciągłości wnękowe powstające w wyniku uwięzienia gazu podczas krzepnięcia, to powszechna, ale uciążliwa wada spawania MIG, która ma kilka przyczyn. Może pojawić się w zastosowaniach półautomatycznych lub zrobotyzowanych i w obu przypadkach wymaga usunięcia i przeróbki – co prowadzi do przestojów i zwiększonych kosztów.
Główną przyczyną porowatości podczas spawania stali jest azot (N2), który dostaje się do jeziorka spawalniczego. Kiedy zbiornik cieczy ochładza się, rozpuszczalność N2 znacznie się zmniejsza i N2 wydostaje się ze stopionej stali, tworząc pęcherzyki (pory). Podczas spawania cynkowanego/galwanizowanego odparowany cynk może zostać wmieszany do jeziorka spawalniczego i jeśli nie ma wystarczającego czasu na ucieczkę przed zestaleniem jeziorka, tworzy się porowatość. W przypadku spawania aluminium cała porowatość jest spowodowana przez wodór (H2), w taki sam sposób, jak N2 działa w stali.
Porowatość spawalnicza może pojawiać się zewnętrznie lub wewnętrznie (często nazywana porowatością podpowierzchniową). Może również rozwijać się w jednym miejscu spoiny lub na całej jej długości, powodując słabe spoiny.
Wiedza o tym, jak zidentyfikować kluczowe przyczyny porowatości i jak szybko je rozwiązać, może pomóc w poprawie jakości, produktywności i wynikach finansowych.
Słaby zasięg gazu osłonowego
Słabe pokrycie gazem osłonowym jest najczęstszą przyczyną porowatości spawania, ponieważ umożliwia zanieczyszczenie jeziorka przez gazy atmosferyczne (N2 i H2). Brak odpowiedniego pokrycia może mieć kilka przyczyn, w tym między innymi słabe natężenie przepływu gazu osłonowego, nieszczelności w kanale gazowym lub zbyt duży przepływ powietrza w komorze spawalniczej. Przyczyną może być także zbyt duża prędkość jazdy.
Jeśli operator podejrzewa, że przyczyną problemu jest słaby przepływ, spróbuj wyregulować przepływomierz gazu, aby upewnić się, że natężenie przepływu jest odpowiednie. Na przykład podczas korzystania z trybu przenoszenia natryskowego powinien wystarczyć przepływ od 35 do 50 stóp sześciennych na godzinę (cfh). Spawanie przy wyższych natężeniach prądu wymaga zwiększenia natężenia przepływu, ale ważne jest, aby nie ustawiać zbyt wysokiego natężenia przepływu. Może to powodować turbulencje w niektórych konstrukcjach pistoletów, które zakłócają pokrycie gazem osłonowym.
Należy pamiętać, że pistolety o różnej konstrukcji mają różną charakterystykę przepływu gazu (patrz dwa przykłady poniżej). „Najlepszy punkt” natężenia przepływu gazu w przypadku górnej konstrukcji jest znacznie większy niż w przypadku dolnej konstrukcji. Jest to kwestia, którą inżynier spawalnik musi wziąć pod uwagę podczas ustawiania komory spawalniczej.
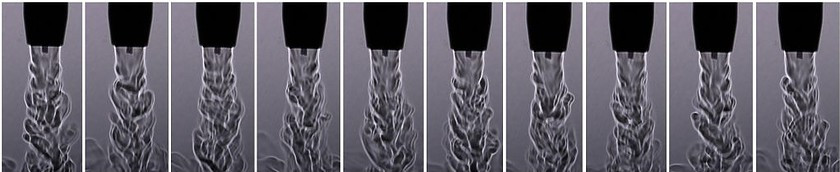
Rysunek 1 przedstawia płynny przepływ gazu na wylocie dyszy
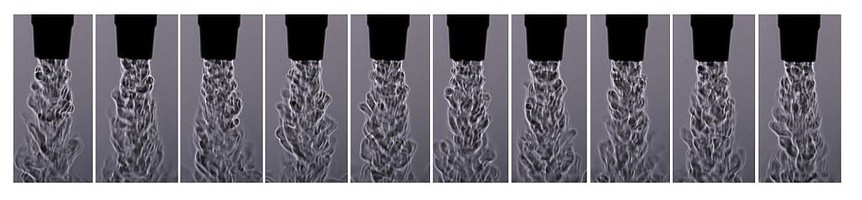
Rysunek 2 przedstawia turbulentny przepływ gazu na wylocie dyszy.
Sprawdź także, czy wąż gazowy, złączki i złączki nie są uszkodzone, a także pierścienie uszczelniające na wtyczce zasilania uchwytu spawalniczego MIG. W razie potrzeby wymienić.
Używając wentylatorów do chłodzenia operatorów lub części w komorze spawalniczej, należy uważać, aby nie były one skierowane bezpośrednio na obszar spawania, gdzie mogłyby zakłócić osłonę gazową. Umieść ekran w komorze spawalniczej, aby chronić przed zewnętrznym przepływem powietrza.
Ponownie dotknij programu w zastosowaniach robotycznych, aby upewnić się, że odległość robocza końcówki od końcówki wynosi zwykle od ½ do 3/4 cala, w zależności od pożądanej długości łuku.
Na koniec, jeśli porowatość utrzymuje się, należy zmniejszyć prędkość przesuwu lub skonsultować się z dostawcą uchwytu MIG w sprawie innych komponentów czołowych z lepszym pokryciem gazowym
Zanieczyszczenie metalami nieszlachetnymi
Zanieczyszczenie metalami nieszlachetnymi to kolejna przyczyna powstawania porowatości – od oleju i smaru po zgorzelinę walcowniczą i rdzę. Wilgoć może również powodować tę nieciągłość, zwłaszcza podczas spawania aluminium. Tego typu zanieczyszczenia zazwyczaj prowadzą do porowatości zewnętrznej widocznej dla operatora. Stal ocynkowana jest bardziej podatna na porowatość podpowierzchniową.
Aby zapobiec porowatości zewnętrznej, należy dokładnie oczyścić materiał podstawowy przed spawaniem i rozważyć użycie drutu spawalniczego z rdzeniem metalowym. Ten typ drutu ma wyższą zawartość odtleniaczy niż drut lity, dzięki czemu jest bardziej tolerancyjny na wszelkie zanieczyszczenia pozostałe na materiale podstawowym. Zawsze przechowuj te i inne przewody w suchym, czystym miejscu o temperaturze podobnej lub nieco wyższej niż temperatura instalacji. Pomoże to zminimalizować kondensację, która mogłaby wprowadzić wilgoć do jeziorka spawalniczego i spowodować porowatość. Nie przechowuj przewodów w chłodni ani na zewnątrz.
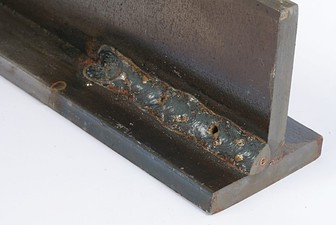
Porowatość, czyli nieciągłości wnękowe powstające w wyniku uwięzienia gazu podczas krzepnięcia, to powszechna, ale uciążliwa wada spawania MIG, która ma kilka przyczyn.
Podczas spawania stali ocynkowanej cynk odparowuje w niższej temperaturze niż topi się stal, a duże prędkości posuwu zwykle powodują szybkie zamarzanie jeziorka spawalniczego. Może to spowodować uwięzienie oparów cynku w stali, powodując porowatość. Aby temu zaradzić, należy monitorować prędkość jazdy. Ponownie rozważ specjalnie zaprojektowany drut metalowy (o formule topnika), który ułatwia ucieczkę oparów cynku z jeziorka spawalniczego.
Zatkane i/lub zbyt małe dysze
Zatkane i/lub zbyt małe dysze mogą również powodować porowatość. Odpryski spawalnicze mogą gromadzić się w dyszy oraz na powierzchni końcówki prądowej i dyfuzorze, powodując ograniczenie przepływu gazu osłonowego lub jego turbulencję. W obu sytuacjach jeziorko spawalnicze pozostaje nieodpowiednio zabezpieczone.
Sytuację tę pogarsza także dysza, która jest za mała do danego zastosowania i jest bardziej podatna na większe i szybsze gromadzenie się odprysków. Mniejsze dysze mogą zapewnić lepszy dostęp do złącza, ale także utrudniać przepływ gazu ze względu na mniejszą powierzchnię przekroju poprzecznego dopuszczalną dla przepływu gazu. Zawsze należy pamiętać o zmiennej odległości końcówki stykowej od wystającej części dyszy (lub wgłębieniu), ponieważ może to być kolejny czynnik wpływający na przepływ gazu osłonowego i porowatość przy wyborze dyszy.
Mając to na uwadze, upewnij się, że dysza jest wystarczająco duża dla danego zastosowania. Zazwyczaj zastosowania z wysokim prądem spawania i użyciem drutu o większym rozmiarze wymagają dyszy o większym rozmiarze otworu.
W przypadku spawania półautomatycznego należy okresowo sprawdzać, czy w dyszy nie ma odprysków spawalniczych i usuwać je za pomocą szczypiec spawalniczych (welperów) lub w razie potrzeby wymienić dyszę. Podczas tej kontroli należy sprawdzić, czy końcówka prądowa jest w dobrym stanie i czy dyfuzor gazu ma czyste porty gazowe. Operatorzy mogą również użyć środka przeciwodpryskowego, muszą jednak uważać, aby nie zanurzyć dyszy w środku zbyt głęboko lub na zbyt długo, ponieważ nadmierne ilości środka mogą zanieczyścić gaz osłonowy i uszkodzić izolację dyszy.
W przypadku spawania zrobotyzowanego zainwestuj w stację do czyszczenia dysz lub rozwiertak, aby zapobiec gromadzeniu się odprysków. To urządzenie peryferyjne czyści dyszę i dyfuzor podczas rutynowych przerw w produkcji, dzięki czemu nie wpływa to na czas cyklu. Stanowiska do czyszczenia dysz przeznaczone są do współpracy z rozpylaczem antyodpryskowym, który nanosi cienką warstwę pasty na przednie elementy. Za dużo lub za mało płynu przeciwodpryskowego może skutkować dodatkową porowatością. Dodanie podmuchu powietrza do procesu czyszczenia dyszy może również pomóc w usunięciu luźnych odprysków z materiałów eksploatacyjnych.
Utrzymanie jakości i produktywności
Dbając o monitorowanie procesu spawania i znając przyczyny porowatości, wdrożenie rozwiązań jest stosunkowo proste. Może to pomóc w zapewnieniu dłuższego czasu zaświecenia łuku, wysokiej jakości wyników i większej liczby dobrych części przechodzących przez produkcję.
Czas publikacji: 02 lutego 2020 r